In an industrial space, lighting doesn’t just need to look good and illuminate a space. It has to stand up to some pretty harsh conditions without presenting safety concerns.
Hazardous location lighting needs to resist fixture surface corrosion from gases like chlorine, Saline, chemicals, and fixture degradation from liquids and corrosives, like those used in food processing sanitation shifts, and it must prevent ignition beyond the rated flash point when used around flammable gases, vapors, dust, or fibers.
Here’s what you need to know to recommend and install safe lighting in these high-risk settings.
What Are Hazardous Locations?
A hazardous location is an environment where materials are being used that could cause a fire or explosion when interacting with the heat or spark of a lighting fixture due to:
- Ambient temperature
- Gases
- Flammability
These locations are prevalent in industries like:
- Refineries
- Petrochemical plants
- Paint booths
- Mining operations
- Animal processing plants
- Agriculture
To help you navigate these risks, hazardous locations are classified into three classes, depending on the hazardous conditions you might encounter there:
Class I Environments | Class II Environments | Class III Environments |
These contain flammable gases and vapors in concentrations sufficient to ignite. Examples include gas stations, paint shops, chemical plants, and alcohol production facilities. | These are characterized by the presence of combustible dust that could ignite. This includes places like candy factories, coal mines, agriculture products (grain, fertilizer) and pharmaceutical manufacturing facilities. | These have ignitable fibers in amounts that could cause ignition, such as in cotton gins and leather goods manufacturing areas (like those producing shoes and handbags). |
These classes are then further divided based on the prevalence of hazardous materials in the area:
Division I: This division indicates that ignitable substances are regularly present during normal operations or could be released in the event of equipment failure, cleaning, etc. |
Division II: This division signifies that ignitable substances exist but are managed, possibly through containment systems like ventilation. |
The Occupational Safety and Health Administration (OSHA) also further categorizes lighting for each class and division into one of the groups from A-G, defined by the specific characteristics of the hazardous materials present.
Class I: These groups cover gases and are sorted from A-D, with Group A gases being the most volatile (most likely to explode, for instance) and Group D the least (such as propane). |
Class II: These groups deal with dusts (as mentioned) and are organized from E-G, where Group E includes dusts with more hazardous/conductive properties, and G indicates dusts with less hazardous properties, etc. |
Selecting the Right Hazardous Location Fixtures
To choose the appropriate LED fixtures for the hazardous location you’re working in, you must understand the specific risks and environmental conditions of the site. You’ll have to consider factors like:
- The type of hazardous material present
- The operating temperature and flash point
- The physical conditions of the environment
To ensure the correct lighting fixtures are used within hazardous settings, various industry groups and regulatory bodies have established standards and certifications.
- The National Fire Protection Association (NFPA) is a nonprofit focused on fire, electrical, life-safety and related hazards. The NFPA’s 275+ codes and standards cover virtually every building, process, service, and design in the country.
- The NFPA codes related to electrical wiring and equipment are the National Electrical Code and the Canadian equivalent, the Canadian Electrical Code. These codes classify risk levels for hazardous location lighting.
- Finally, OSHA, of the U.S. Department of Labor, enforces regulations to ensure safe and healthy workplaces.
Certifications for Hazardous Location Lighting
Certifications ensuring safety in hazardous locations include:
- ATEX:The ATEX Directive includes two key European Union directives focusing on explosion-proof lighting and other equipment and protective systems created for use in potentially explosive environments. It outlines essential health and safety requirements, certification processes, and conformity assessment procedures. ATEX certification is mandatory within the EU.
- The IECEx system offers a means to prove compliance with international standards for equipment used in explosive atmospheres. It involves a certification process whereby equipment is tested and verified against the IEC standards, specifically the IEC 60079 and IEC 61241 series prepared by technical committee 31. Achieving IECEx certification indicates that a product can safely be used in hazardous locations and meets global requirements.
- UL Solutions offers certification and advisory services for hazardous locations (HazLoc), helping manufacturers navigate global compliance requirements. Certifications include UL, C-UL, ATEX, IECEx, and more.
Various petrochemical certifications may also apply, depending on the kinds of chemicals used in the space.
Challenges and Innovative Solutions for Harsh Environments
The biggest challenge in hazardous location lighting is dealing with extreme temperatures and corrosive substances. For instance, in high-heat environments like aluminum recycling plants, finding LED fixtures that can withstand the temperatures over furnaces is difficult. Similarly, in locations with saline or chlorine, such as indoor swimming pools, corrosion-resistant fixtures are essential.
Advancements in technology have led to the development of lighting solutions that are not only energy-efficient but also capable of withstanding harsh conditions. These include corrosion-resistant fixtures and LEDs designed for extreme temperatures.
Product Spotlight: Hazardous Location LED Lighting
Our highly efficient, safety-focused LED High Bay for high-ceiling, hazardous locations.
These LED light fixtures for high ceilings were designed to minimize fire and explosion risks in industrial settings.
- Class I, Division 2 rating guarantees the fixture meets national safety standards.
- T4 rating ensures a low operating temperature, further reducing the risk of ignition.
- Corrosion-resistant coating keeps the fixture protected from corrosive materials.
- IP66 rating keeps the fixture resistant to dust or nozzle-projected water.
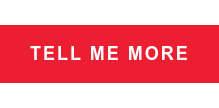
Trends in Hazardous Location Lighting
With all the demands of hazardous location lighting, the trends surrounding it tend to focus on a shift toward more versatile and durable options.
Because hazardous lighting LEDs must meet such strict specifications, builders and contractors don’t have many options that meet all their needs. Looking ahead, hazardous location fixtures will also incorporate other options, such as:
- Enhanced energy efficiency
- Integration of smart controls and sensors for enhanced safety and operational efficiency
- Expanded choice of lumen packages and form factors, including round and linear options, and various mounting methods
- Utilizing motion sensing rated for Hazardous Locations.
- Fixtures that operate at higher voltages and withstand higher temperatures, thus improving longevity.
Understanding the complexities of lighting in hazardous areas is crucial for maintaining workplace safety and meeting regulations. Consulting regulations help ensure you select the right lighting solutions, balancing safety with efficiency. As technologies and standards evolve, you’ll have more options to balance safety with energy efficiency, style, and other concerns, making choosing the right lighting easier than ever.